图书介绍
热加工工艺规范2025|PDF|Epub|mobi|kindle电子书版本百度云盘下载
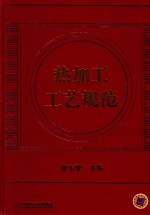
- 樊东黎主编 著
- 出版社: 北京:机械工业出版社
- ISBN:7111110889
- 出版时间:2003
- 标注页数:1322页
- 文件大小:911MB
- 文件页数:1341页
- 主题词:热加工
PDF下载
下载说明
热加工工艺规范PDF格式电子书版下载
下载的文件为RAR压缩包。需要使用解压软件进行解压得到PDF格式图书。建议使用BT下载工具Free Download Manager进行下载,简称FDM(免费,没有广告,支持多平台)。本站资源全部打包为BT种子。所以需要使用专业的BT下载软件进行下载。如BitComet qBittorrent uTorrent等BT下载工具。迅雷目前由于本站不是热门资源。不推荐使用!后期资源热门了。安装了迅雷也可以迅雷进行下载!
(文件页数 要大于 标注页数,上中下等多册电子书除外)
注意:本站所有压缩包均有解压码: 点击下载压缩包解压工具
图书目录
第1篇 热加工工艺基础及综合资料1
第1章 铸造工艺基础及综合资料1
1 金相组织1
1.1 铁碳合金相图1
1.2 铸铁金相组织及控制范围3
1.3 铸钢组织9
2 铸铁10
2.1 铸铁的分类10
2.2 铸铁牌号表示方法10
2.3 铸铁化学成分和力学性能11
3 铸钢25
3.1 铸钢的分类和应用25
3.2 铸钢牌号表示方法25
3.3 铸钢化学成分和力学性能26
4 铸造非铁合金32
4.1 铸造非铁合金的分类32
4.2 铸造非铁纯金属及其合金牌号表示方法32
4.3 铸造非铁合金的化学成分和力学性能33
5 铸造工艺45
5.1 铸造工艺设计45
5.2 铸件结构的工艺性50
5.3 铸造工艺方案的确定58
5.4 铸造工艺参数62
6 铸造常用原辅材料70
6.1 金属炉料70
6.2 燃料、熔剂和修炉用的耐火材料91
6.3 造型材料100
参考文献104
第2章 热塑性成形工艺基础105
1 金属结构105
1.1 晶格构造105
1.2 金属的晶体结构106
2 塑性加工过程中的力106
2.1 外力106
2.2 内力和应力107
3 金属变形及金属塑性107
3.1 金属变形及其形式107
3.2 变形程度107
3.3 塑性与变形抗力108
4 塑性变形的物理基础108
4.1 单晶体的变形过程及其实质108
4.2 多晶体变形的方式和特点110
4.3 多晶体的加工硬化111
5 硬化金属的软化过程112
5.1 回复阶段113
5.2 再结晶阶段113
5.3 晶粒长大阶段114
6 影响金属塑性的因素114
6.1 金属组织及化学成分对塑性的影响114
6.2 变形温度和应变速率对塑性的影响116
6.3 应力状态对塑性的影响118
7 塑性加工中的摩擦及其对金属塑性变形过程的影响120
7.1 塑性加工中摩擦的特点120
7.2 摩擦对塑性变形过程的影响120
8 金属塑性变形的基本定律121
8.1 切应力定律121
8.2 金属塑性变形时存在弹性变形的定律121
8.3 体积不变条件122
8.4 最小阻力定律122
9 热变形对金属组织和性能的影响123
9.1 热变形对金属组织的影响123
9.2 热变形对金属性能的影响124
10 锻造用钢125
10.1 钢的冶炼方法简介125
10.2 钢锭的型式、组织与缺陷125
10.3 钢坯及其缺陷127
11 金属加热128
11.1 金属锻前加热的目的128
11.2 钢在加热时易出现的缺陷及防止方法128
11.3 金属加热方法及其设备特点128
11.4 敞焰少氧化加热原理简介129
12 锻件冷却及热处理130
12.1 冷却对锻件质量的影响130
12.2 锻件的冷却130
12.3 锻件热处理的目的和种类130
13 几种特种热成形工艺基础简介133
13.1 金属等温成形工艺133
13.2 金属超塑性成形工艺136
13.3 金属液态模锻工艺141
13.4 金属粉末锻造工艺147
参考文献150
第3章 焊接与切割工艺基础151
1 焊割方法分类151
2 焊割方法概述151
2.1 焊条电弧焊(原称手工电弧焊)151
2.2 埋弧焊151
2.3 钨极氩弧焊152
2.4 熔化极气体保护焊152
2.5 等离子弧焊接与切割152
2.6 气焊与气割152
2.7 电渣焊152
2.8 电阻焊153
2.9 电子束焊153
2.10 激光焊接与切割153
2.11 摩擦焊153
2.12 钎焊154
2.13 堆焊154
2.14 高频焊154
2.15 气压焊154
2.16 热剂焊(常称铝热焊)154
2.17 爆炸焊154
2.18 冷压焊154
2.19 超声波焊155
2.20 扩散焊155
2.21 螺柱焊155
2.22 水下焊155
2.23 热喷涂155
3 焊接电弧155
3.1 带电粒子的产生156
3.2 电弧电压和弧长156
3.3 电弧静特性曲线156
3.4 电弧温度157
3.5 交流电弧157
3.6 拘束电弧157
3.7 电弧的磁偏吹157
4 熔焊冶金过程特点157
4.1 焊条(丝)熔化与过渡158
4.2 气体对金属的作用158
4.3 熔渣与金属的作用162
4.4 焊接熔池的一次结晶164
4.5 偏析、夹杂和气孔165
4.6 熔合区的不均匀性166
4.7 焊缝金属的二次结晶166
4.8 热影响区的组织与性能166
4.9 裂纹167
5 焊接材料169
5.1 焊条169
5.2 焊丝173
5.3 焊剂176
5.4 钎料180
5.5 钎剂182
5.6 保护气体184
5.7 氧气与燃气186
6 弧焊电源选用技术基础187
6.1 弧焊电源外特性187
6.2 弧焊电源与电弧的稳定工作点189
6.3 弧焊电源的调节特性189
6.4 弧焊电源的动特性190
6.5 弧焊电源的空载电压191
6.6 负载持续率(FC)191
7 金属材料的焊接性与常用金属材料焊接要点192
7.1 焊接性的概念192
7.2 常用金属材料焊接要点192
8 预热、后热及焊后热处理200
8.1 预热200
8.2 后热201
8.3 焊后热处理201
8.4 实施方法202
9 焊接结构工艺性202
9.1 合理选择焊接结构材料202
9.2 合理布置焊接结构上的焊缝203
9.3 合理选用焊接接头205
10 质量检验方法205
10.1 非破坏性检验205
10.2 破坏性试验208
11 安全技术基础212
11.1 燃烧与火灾212
11.2 爆炸213
11.3 触电213
11.4 电焊烟尘及有毒气体214
11.5 弧光辐射215
11.6 放射线伤害215
11.7 高频电磁场215
11.8 噪声215
参考文献215
第4章 热处理工艺基础217
1 金属热处理工艺分类和代号217
1.1 基础分类217
1.2 附加分类217
1.3 热处理工艺代号217
1.4 常用热处理工艺代号举例218
2 热处理可控气氛的分类和代号219
2.1 各国可控气氛的分类和代号219
2.2 我国的可控气氛分类和代号220
2.3 可控气氛分类代号与典型气氛组分、用途221
3 热处理炉有效加热区的测定222
3.1 有效加热区测定的必要性222
3.2 有效加热区的测定方法222
3.3 有效加热区测定结果的评定223
4 钢的热处理基础223
4.1 钢号命名法223
4.2 钢在各种状态下的组织224
4.3 钢的过冷奥氏体转变227
4.4 钢的热处理基本工艺229
4.5 离子热处理240
4.6 高密度能加热表面热处理242
4.7 钢的热处理基础数据243
5 铸铁的热处理基础281
5.1 铸铁的分类及代号281
5.2 铸铁固态相变特征和常温下的组织282
5.3 铸铁热处理基本工艺284
6 非铁合金的热处理285
6.1 非铁合金说明及代号285
6.2 铝合金的热处理287
6.3 铜及铜合金的热处理289
6.4 镍及镍合金的热处理291
6.5 钛及钛合金的热处理291
6.6 镁及镁合金的热处理292
7 金属热处理的加热294
7.1 加热介质的分类294
7.2 金属在各种介质中加热时的行为295
7.3 不同介质中的加热计算公式299
7.4 加热的节能措施303
7.5 可控气氛304
7.6 加热熔盐和流态床322
7.7 金属在真空中的加热331
8 金属热处理的冷却333
8.1 金属热处理的冷却过程333
8.2 钢的热处理冷却334
8.3 钢的淬透性337
8.4 钢的淬透性曲线346
8.5 淬火冷却介质370
8.6 钢件淬火时的畸变与开裂396
9 热处理生产中的安全卫生要求400
9.1 热处理生产安全卫生的重要性400
9.2 热处理生产中的危险因素与有害因素401
9.3 热处理厂房和作业环境407
9.4 生产物料和剩余物料411
9.5 生产装置安全事项411
9.6 热处理工艺作业安全卫生423
9.7 热处理安全、卫生防护技术措施425
9.8 安全卫生的管理426
10 热处理标准一览表427
参考文献428
第2篇 铸造工艺规范429
第1章 铸造用模样制造工艺规范429
1 木模样制造工艺规范429
1.1 制造木模样用材429
1.2 木模样(含芯盒)等级及技术条件429
1.3 木模样制造工艺431
1.4 涂漆435
1.5 木模样的质量检验和保管435
2 金属模样制造工艺规范435
2.1 金属模样材料、结构及技术要求435
2.2 金属模样制造工艺440
3 塑料模样制造工艺规范442
3.1 环氧塑料模样制造工艺规范442
3.2 聚苯乙烯泡沫塑料模样制造452
4 快速成型制造模样454
参考文献455
第2章 型砂、芯砂及涂料配制工艺规范456
1 以粘土为粘结剂的型砂和芯砂配制工艺规范456
1.1 粘土砂原材料的准备及选用456
1.2 型砂、芯砂配比及性能456
1.3 粘土砂配制工艺460
2 以油类为粘结剂的芯砂配制工艺规范460
2.1 以植物油为粘结剂的芯砂配制工艺规范460
2.2 以合脂为粘结剂的芯砂配制工艺规范461
3 以树脂为粘结剂的型砂、芯砂配制工艺规范462
3.1 呋喃树脂自硬砂配制工艺规范462
3.2 热芯盒树脂砂配制工艺规范464
3.3 壳型(芯)砂配制工艺规范466
3.4 冷芯盒树脂砂配制工艺规范467
4 以水泥为粘结剂的型砂、芯砂配制工艺规范469
4.1 特快硬矾土水泥自硬砂配制工艺规范469
4.2 双快水泥自硬砂配制工艺规范470
5 以水玻璃为粘结剂的型砂、芯砂配制工艺规范471
5.1 水玻璃CO2硬化砂471
5.2 加热硬化水玻璃砂472
5.3 水玻璃有机酯自硬砂472
6 以石灰石为原砂、水玻璃为粘结剂的型砂、芯砂配制工艺规范473
6.1 石灰石水玻璃砂原材料的选用与准备473
6.2 石灰石水玻璃砂的配制473
7 型砂、芯砂混制生产安全通则474
8 涂料配制与使用工艺规范474
8.1 涂料配制工艺规范474
8.2 涂料的使用方法476
参考文献477
第3章 造型、造芯、烘干工艺规范478
1 生产技术准备工艺规范478
1.1 芯骨制造工艺规范478
1.2 芯撑479
1.3 冷铁479
1.4 工艺装备479
2 手工造型工艺规范480
2.1 粘土砂湿型、干型造型工艺规范480
2.2 粘土砂地坑造型工艺规范483
3 自硬砂造型(芯)工艺规范485
3.1 呋喃树脂自硬砂造型(芯)工艺规范485
3.2 双快水泥自硬砂造型(芯)工艺规范486
4 水玻璃砂造型(芯)工艺规范486
4.1 水玻璃CO2硬化砂造型(芯)工艺规范486
4.2 水玻璃有机酯自硬砂造型(芯)工艺规范488
4.3 石灰石水玻璃砂造型(芯)工艺规范488
5 机器造型工艺规范489
5.1 机器造型通用工艺规范489
5.2 震实机械造型工艺规范490
5.3 震压机械脱箱造型工艺规范490
5.4 射压、高压、微震造型线工艺规范490
5.5 抛砂机造型工艺规范491
6 砂芯制造工艺规范491
6.1 砂芯制造通用技术要求491
6.2 粘土砂手工造芯工艺规范491
6.3 机器造芯工艺规范492
6.4 热芯盒制芯工艺规范493
6.5 冷芯盒制芯工艺规范493
6.6 壳型工艺制芯(型)工艺规范494
6.7 自硬砂制芯工艺规范495
6.8 砂芯快速成型495
7 砂型、砂芯烘干工艺规范496
7.1 砂型、砂芯烘干质量要求496
7.2 室式电阻烘干炉砂芯烘干典型工艺规范496
7.3 立式烘干炉砂芯烘干典型工艺规范497
7.4 室式烘干炉砂型及砂芯烘干工艺规范498
参考文献500
第4章 铸铁熔炼、浇注工艺规范501
1 冲天炉熔炼工艺规范501
1.1 材料准备及管理501
1.2 炉、包修搪工艺504
1.3 冲天炉熔炼工艺506
2 感应电炉熔炼工艺规范509
2.1 无心感应电炉熔炼工艺规范509
2.2 有心感应电炉熔炼工艺规范515
3 典型铸铁熔炼工艺规范519
3.1 孕育铸铁熔炼工艺规范519
3.2 球墨铸铁熔炼工艺规范528
3.3 蠕墨铸铁熔炼工艺规范538
3.4 可锻铸铁熔炼工艺规范545
4 常用合金铸铁熔炼工艺规范553
4.1 耐磨铸铁熔炼工艺规范555
4.2 抗磨铸铁熔炼工艺规范557
4.3 耐热铸铁熔炼工艺规范564
4.4 耐蚀铸铁熔炼工艺规范566
5 浇注工艺规范569
5.1 浇注前的准备569
5.2 浇注570
5.3 安全生产570
5.4 浇注记录570
参考文献570
第5章 铸钢熔炼、浇注工艺规范571
1 电弧炉熔炼工艺规范571
1.1 碱性电弧炉熔炼工艺规范571
1.2 酸性电弧炉熔炼工艺规范575
2 感应电炉熔炼工艺规范576
2.1 碱性感应电炉熔炼工艺规范576
2.2 酸性感应电炉熔炼工艺规范577
3 平炉熔炼工艺规范578
3.1 碱性平炉熔炼工艺规范578
3.2 酸性平炉熔炼工艺规范580
4 钢包精炼炉熔炼工艺(ASEA-SKF精炼炉)582
5 典型钢种熔炼工艺规范(碱性电弧炉熔炼)583
5.1 碳钢熔炼工艺规范583
5.2 低合金钢熔炼工艺规范584
5.3 铬镍不锈钢熔炼工艺规范585
5.4 高锰钢熔炼工艺规范585
6 铸钢浇注工艺规范586
6.1 浇注前的准备586
6.2 浇注586
6.3 安全生产587
6.4 浇注记录587
参考文献588
第6章 铸造非铁合金熔炼工艺规范589
1 铸造铝合金熔炼工艺规范589
2 铸造铜合金熔炼工艺规范601
3 压铸用铝合金熔炼工艺规范611
3.1 总则611
3.2 准备611
3.3 合金的熔炼612
3.4 质量检查及操作记录613
3.5 安全技术613
4 铸造镁合金熔炼工艺规范613
5 铸造锌合金熔炼工艺规范620
6 铸造纯钛和钛合金熔炼工艺规范622
7 铸造轴承合金熔炼工艺规范626
参考文献629
第7章 特种铸造工艺规范630
1 熔模铸造工艺规范630
1.1 总则630
1.2 熔模制造630
1.3 型壳制造634
1.4 合金熔炼和浇注641
1.5 铸件清理和入库641
1.6 安全生产642
2 金属型铸造工艺规范642
3 压力铸造工艺规范646
4 低压铸造工艺规范648
5 离心铸造工艺规范651
5.1 套、筒类铸件离心铸造工艺规范651
5.2 双金属轴瓦离心铸造工艺规范653
6 其他特种铸造工艺规范653
6.1 真空吸铸工艺规范653
6.2 挤压铸造工艺规范654
6.3 陶瓷型铸造工艺规范654
6.4 实型负压铸造工艺规范656
参考文献658
第8章 铸件清理、检验、修补及涂底漆工艺规范659
1 铸铁件清理、检验及修补工艺规范659
1.1 铸铁件清理工艺规范659
1.2 铸铁件检验663
1.3 铸铁件缺陷修补工艺规范665
2 铸钢件清理、气割及焊补工艺规范669
2.1 铸钢件清理工艺规范669
2.2 铸钢件气割工艺规范670
2.3 铸钢件焊补工艺规范675
3 铸铁、铸钢件防锈涂漆工艺规范675
3.1 技术要求675
3.2 工艺规范675
3.3 检查注意事项676
3.4 安全生产676
4 铸件存放676
参考文献676
第9章 铸件热处理工艺规范677
1 铸铁件热处理工艺规范677
1.1 灰铸铁件热处理工艺规范677
1.2 球墨铸铁件热处理工艺规范679
1.3 可锻铸铁件热处理工艺规范682
2 铸钢件的热处理工艺规范686
2.1 碳钢铸件的热处理工艺规范686
2.2 低合金钢铸件热处理工艺规范689
2.3 高锰钢铸件热处理工艺规范690
2.4 不锈钢铸件热处理工艺规范691
3 非铁合金铸件热处理工艺规范693
参考文献693
第3篇 锻压工艺规范694
第1章 锻压原材料的标识、检验和下料694
1 锻压原材料的标识规定694
1.1 常用钢铁材料的涂色标识694
1.2 常用非铁金属材料的涂色标识695
2 锻压原材料的检验要点与规范696
2.1 钢铁合金铸锭的检验要点696
2.2 非铁合金铸锭的检验要点696
2.3 锻坯质量的检验要点696
2.4 轧材质量的检验要点697
2.5 挤压棒、型材质量的检验要点698
3 部分钢材的火花鉴别法698
3.1 火花的构成及其表征699
3.2 钢中合金元素对火花的影响700
3.3 部分钢材的火花特征701
4 锻压原材料下料规范705
4.1 锻造工艺对下料质量的要求705
4.2 锻件毛坯下料的通用技术条件705
4.3 棒料剪切下料安全操作规范706
4.4 金属材料进行氧气切割下料的条件706
第2章 原材料锻前加热规范708
1 钢锭的加热规范708
1.1 钢锭加热规范的类型708
1.2 热钢锭加热操作要点708
1.3 冷钢锭加热规范示例和规范708
2 钢坯的加热规范710
2.1 钢坯加热操作要点710
2.2 一些钢种钢坯的加热规范710
3 高温合金及非铁合金的加热规范711
3.1 高温合金加热规范711
3.2 铝合金加热规范712
3.3 镁合金加热规范712
3.4 钛合金加热规范713
3.5 铜合金加热规范714
4 锻造加热炉安全操作规程714
4.1 煤气加热炉安全操作规程714
4.2 重油加热炉安全操作规程715
4.3 电炉加热安全操作规程715
第3章 热塑性成形工艺规范716
1 自由锻造工序的操作要点和规则716
1.1 拔长工序的操作要点和规则716
1.2 芯棒拔长的操作要点和规则719
1.3 镦粗工序的操作要点和规则720
1.4 冲孔工序的操作要点和规则721
1.5 扩孔工序的操作要点和规则721
1.6 滚圆工序的操作要点和规则722
1.7 弯曲工序的操作要点和规则723
1.8 扭转工序的操作要点和规则723
1.9 切割工序的操作要点和规则724
1.10 错移工序的操作要点和规则725
1.11 锻接工序的操作要点和规则725
2 锻造操作中的规范手示信号725
2.1 水压机锻造操作中的手示信号725
2.2 自由锻锤操作中的手示信号726
3 常用金属材料的热锻操作要点和规则726
3.1 常用低、中碳钢和低合金钢的热锻特点726
3.2 常用高合金钢的热锻特点727
3.3 常用特殊钢的热锻特点727
3.4 非铁合金的热锻特点731
4 模锻件加工余量及公差和模锻件图的建立732
4.1 钢质模锻件公差及加工余量标准732
4.2 锻件图设计与画法守则741
5 模锻工序的操作要点与规则745
5.1 制坯工序747
5.2 模锻工序748
6 其他模锻工序的操作要点与规则749
6.1 高速锤模锻工艺过程规范749
6.2 等温锻造工艺过程规范751
6.3 钢质液态模锻工艺操作规范754
6.4 辊锻工艺过程规范756
第4章 锻件锻后冷却、热处理及检验规范759
1 锻后冷却规范759
1.1 锭制锻件锻后冷却规范759
1.2 轧材或锻坯制锻件锻后冷却规范761
2 锻后热处理规范763
2.1 锭制大锻件的锻后热处理规范763
2.2 中、小型锻件锻后热处理规范770
2.3 锻件锻后冷却及热处理工艺规范794
3 锻件质量检验规范795
3.1 常见锻件的质量检验项目795
3.2 各类锻件检验要求细则796
3.3 锻件外观质量检验守则798
3.4 锤锻锻件质量等级判定的一般规范800
第5章 锻模制造、检验与设备使用规范803
1 锻模制造与检验规范803
1.1 锻模加工工艺规范803
1.2 锻模热处理工艺规范806
1.3 锻模检验规范809
2 锻造设备的操作和使用规范810
2.1 空气锤的操作和使用要点810
2.2 蒸—空两用自由锻锤的操作使用要点811
2.3 自由锻造水压机的操作使用要点813
2.4 辊锻机的操作使用要点813
2.5 其他一些锻压设备的操作要点815
第6章 锻造车间管理、安全、环保规范817
1 锻造车间管理规范817
1.1 生产技术管理规范817
1.2 生产管理规范817
1.3 锻件生产环节中的质量控制规范817
1.4 锻件回用规范819
2 锻造车间安全生产规范819
2.1 锻造车间安全生产的一般规范819
2.2 锻造车间设备及工具安全使用的一般规范820
2.3 操作工人安全生产规范820
2.4 辅助操作工人安全生产规范822
3 锻造车间作业环境与环保规范825
3.1 锻造车间作业环境规范825
3.2 锻造车间环保基本规范825
3.3 锻造车间噪声及振动控制规范826
3.4 锻造车间废水控制规范827
3.5 锻造车间废气控制规范828
3.6 锻造车间废渣及其他污染控制规范829
参考文献829
第4篇 焊接工艺规范830
第1章 焊条电弧焊830
1 焊条电弧焊设备830
1.1 弧焊电源830
1.2 焊条电弧焊辅助设备833
2 焊条833
2.1 焊条分类、表示方法及型号、牌号对照833
2.2 焊条选用要点834
2.3 焊条的管理与使用834
3 焊条电弧焊工艺834
3.1 焊接接头形式及坡口制备834
3.2 焊前准备836
3.3 焊接参数837
3.4 薄板(厚度≤2mm)焊接工艺839
3.5 板状焊件单面焊双面成形技术839
3.6 水平固定管的焊接工艺841
3.7 垂直固定管的焊接工艺842
3.8 管道的向下立焊法842
3.9 重力焊及高效铁粉焊条焊接工艺844
4 常用材料的焊接工艺845
4.1 低、中碳钢的焊接工艺845
4.2 低合金高强钢焊接工艺845
4.3 低、中合金耐热钢焊接849
4.4 低温钢焊接850
4.5 不锈钢焊接851
4.6 铸铁焊补852
5 焊条电弧焊常见缺陷及防止措施854
6 焊条电弧焊安全技术855
6.1 电焊机使用安全技术855
6.2 焊接电缆使用安全技术855
6.3 焊钳使用安全技术856
6.4 焊接操作中的安全技术856
参考文献856
第2章 埋弧焊857
1 埋弧焊设备857
1.1 弧焊电源857
1.2 埋弧焊机858
1.3 辅助装置及易损件858
2 焊接材料859
2.1 焊丝的选用859
2.2 焊剂类型与焊丝配用859
2.3 焊接材料的管理与使用860
3 埋弧焊工艺860
3.1 焊接接头坡口形式860
3.2 焊前准备863
3.3 焊接参数对焊缝形状的影响863
3.4 各种埋弧焊工艺864
3.5 埋弧焊常见缺陷及防止措施873
3.6 安全技术874
参考文献874
第3章 气体保护电弧焊875
1 钨极氩弧焊875
1.1 钨极氩弧焊特点875
1.2 钨极氩弧焊设备875
1.3 焊接材料的选择879
1.4 钨极氩弧焊工艺880
1.5 手工钨极氩弧焊操作技术884
1.6 特种钨极氩弧焊886
1.7 安全技术887
1.8 生产实例887
2 熔化极氩弧焊888
2.1 MIG焊和MAG焊的特点888
2.2 熔化极氩弧焊设备889
2.3 熔化极氩弧焊工艺892
2.4 熔化极脉冲氩弧焊896
2.5 窄间隙MAG焊899
3 CO2气体保护电弧焊900
3.1 CO2焊的冶金特点900
3.2 CO2焊电弧及熔滴过渡的特点901
3.3 CO2气体保护焊用焊接材料901
3.4 CO2气体保护焊设备的特点902
3.5 CO2气体保护焊焊接工艺903
4 气电立焊908
4.1 气电立焊特点908
4.2 气电立焊设备909
4.3 气电立焊工艺909
参考文献910
第4章 等离子弧焊接与切割911
1 等离子弧焊的工艺特点911
1.1 设备与工装种类及选用912
1.2 接头设计及坡口制备914
1.3 操作过程及焊接参数915
1.4 典型材料及其焊接918
1.5 焊接缺陷及质量检验918
1.6 安全技术919
2 等离子弧切割工艺特点919
2.1 设备与工装种类及选用920
2.2 操作过程及切割参数922
2.3 常用金属材料切割923
2.4 其他类型的等离子弧切割方法925
2.5 缺陷和质量检验926
2.6 安全技术926
参考文献927
第5章 电渣焊928
1 电渣焊焊接参数的选择、设备简介和焊接经验数据汇总928
1.1 焊接参数拟定原则和选择依据928
1.2 焊接参数的拟定930
1.3 设备简介937
1.4 不同构件电渣焊经验数据汇总938
2 电渣焊工艺945
2.1 准备工作945
2.2 操作及焊接参数的控制955
2.3 焊后处理工作957
3 电渣焊工艺中值得注意的几个操作技术难题957
3.1 环缝电渣焊957
3.2 大截面熔嘴电渣焊的引弧造渣961
3.3 弯曲变截面焊件的熔嘴电渣焊962
4 电渣焊接头质量检查、常见的缺陷及其产生原因和防止措施965
4.1 接头质量检验965
4.2 接头中常见的缺陷及其产生原因和防止措施965
5 安全技术967
参考文献967
第6章 气焊、气割与气刨968
1 气焊与气割968
1.1 燃气的选用968
1.2 燃气设备及装置968
1.3 气焊、气割用工具971
2 气焊技术与工艺974
2.1 气焊火焰与材料的选择974
2.2 气焊工艺976
2.3 常用金属材料的气焊978
3 氧气切割982
3.1 气割的基本原理982
3.2 氧气切割工艺984
3.3 其他燃气及热切割方法986
4 碳弧气刨989
4.1 碳弧气刨原理及应用989
4.2 碳弧气刨设备与材料989
4.3 碳弧气刨工艺991
5 气焊、气割安全技术992
5.1 设备及工具的安全使用992
5.2 气焊、气割操作安全与保护992
参考文献993
第7章 电子束焊994
1 工艺特点994
2 设备与工装种类及选用994
3 接头设计及坡口制备996
4 操作过程及焊接参数997
5 常用金属材料焊接998
6 缺陷及质量检验1000
7 安全技术1000
参考文献1000
第8章 激光焊接与切割1001
1 激光焊工艺1001
1.1 工艺特点1001
1.2 设备与工装种类1002
1.3 接头设计及坡口制备1003
1.4 操作过程及焊接参数1003
1.5 常用材料焊接1006
1.6 缺陷及质量检验1007
1.7 安全技术1007
2 激光切割工艺1008
2.1 工艺特点1008
2.2 设备、工装种类及选用1008
2.3 操作过程及焊接参数1009
2.4 常用材料的切割1010
2.5 缺陷及质量检验1012
2.6 安全技术1013
参考文献1013
第9章 电阻焊1014
1 分类1014
2 电阻点焊1014
2.1 电阻点焊过程1014
2.2 点焊方法1016
2.3 接头形式和结构设计1017
2.4 设备及型号编制1018
2.5 电极1020
2.6 焊前准备工作1023
2.7 焊接参数选择1025
2.8 常用金属材料的点焊1025
2.9 缺陷及质量检验1032
2.10 质量监控技术的应用简介1034
3 缝焊1036
3.1 热过程特点1036
3.2 缝焊方法1036
3.3 接头形式及设计1038
3.4 设备及型号编制1038
3.5 工艺及参数1042
3.6 常用金属材料缝焊1042
3.7 缺陷及质量检验1046
4 凸焊1046
4.1 应用及特点1046
4.2 凸焊过程1046
4.3 工艺方法1047
4.4 凸焊接头设计1048
4.5 凸焊设备1049
4.6 凸焊电极及工装1051
4.7 焊接参数1051
4.8 常用金属材料凸焊1052
4.9 缺陷及质量检验1054
5 对焊1055
5.1 电阻对焊1055
5.2 闪光对焊1058
5.3 对焊机1062
5.4 常用金属材料对焊1065
5.5 典型工件对焊1067
5.6 缺陷、质量检验及监控1071
6 安全技术1073
参考文献1073
第10章 摩擦焊1074
1 分类及特点1074
2 设备及工装1074
3 焊接参数1076
3.1 连续驱动摩擦焊焊接参数1076
3.2 惯性摩擦焊的焊接参数1076
4 焊接参数的选择1077
5 接头形式和设计1078
6 摩擦焊实例1079
7 接头质量及控制1080
8 注意事项1081
参考文献1081
第11章 堆焊1082
1 焊条电弧堆焊1082
1.1 特点1082
1.2 堆焊用焊条1082
1.3 堆焊工艺1085
1.4 各类焊条堆焊工艺特点1085
1.5 各类焊条堆焊时的电流值1087
2 氧乙炔焰堆焊1087
2.1 特点1087
2.2 钴基合金氧乙炔焰堆焊1087
2.3 镍基合金氧乙炔焰堆焊1088
2.4 碳化钨合金氧乙炔焰堆焊1088
2.5 黄铜氧、乙炔焰堆焊1089
3 自动埋弧堆焊1089
3.1 特点1089
3.2 自动埋弧堆焊的几种方法1089
3.3 自动埋弧堆焊焊丝、焊带与焊剂的配合方式1089
3.4 汽车、拖拉机零件埋弧堆焊1089
3.5 轧辊埋弧堆焊1090
3.6 不锈钢带极埋弧堆焊1091
4 带极电渣堆焊1092
4.1 概述1092
4.2 核容器不锈钢带极电渣堆焊工艺1092
5 气体保护堆焊及自保护焊丝堆焊1092
5.1 钨极氩弧堆焊(TIG)1092
5.2 熔化极氩弧堆焊(MIG)1093
5.3 CO2气体保护堆焊1093
5.4 自保护药芯焊丝堆焊1093
5.5 振动堆焊1093
6 等离子弧堆焊1094
6.1 特点1094
6.2 等离子弧堆焊的几种方法1094
6.3 等离子弧堆焊用粉末1094
6.4 等离子弧堆焊设备1094
6.5 等离子弧堆焊参数1095
7 电渣堆焊1096
7.1 特点1096
7.2 板极电渣堆焊参数1096
7.3 电渣堆焊使用的设备1097
参考文献1097
第12章 钎焊1098
1 钎料的选用1098
2 去氧化膜1099
2.1 钎剂去氧化膜1099
2.2 其他防氧化方法1099
3 方法及设备1100
3.1 火焰钎焊1100
3.2 炉中钎焊1100
3.3 浸渍钎焊1101
3.4 电阻钎焊1102
3.5 感应钎焊1103
4 接头设计1103
4.1 接头形式及其与载荷的关系1103
4.2 接头间隙1104
5 钎焊前焊件的表面处理1104
5.1 焊件表面脱脂1104
5.2 氧化膜的化学清理1105
5.3 焊件表面镀覆金属层1105
6 工艺1105
6.1 钎料形状及数量的确定1105
6.2 钎料的放置1105
6.3 钎焊参数的确定1106
7 焊后的处理工序1106
7.1 焊后热处理1106
7.2 焊后焊件的清理1107
8 接头缺陷及质量检验1107
8.1 接头的缺陷及防止措施1107
8.2 质量检验1108
9 常用金属材料的钎焊举例1108
9.1 碳钢和低合金钢的钎焊1108
9.2 不锈钢钎焊1109
10 安全技术1109
参考文献1109
第13章 热喷涂1110
1 分类1110
2 火焰线材喷涂1110
2.1 设备1110
2.2 工艺1110
2.3 喷涂用材料1111
3 火焰粉末喷涂1111
3.1 设备1111
3.2 工艺1112
4 火焰粉末喷熔1113
4.1 设备1113
4.2 一步法火焰粉末喷熔工艺1113
4.3 二步法火焰粉末喷熔工艺1113
4.4 火焰喷熔用粉末1114
5 电弧喷涂1114
5.1 设备1114
5.2 喷涂用线材1114
5.3 工艺1114
6 等离子弧喷涂1115
6.1 设备1115
6.2 工艺1115
6.3 喷涂用材料1116
7 涂层性能检验1116
8 安全技术1116
8.1 防爆防火及设备防护1116
8.2 劳动保护1116
参考文献1117
第14章 其他焊接工艺1118
1 水下焊接与切割1118
1.1 水下焊接1118
1.2 水下切割1122
1.3 安全技术及劳动卫生保护1123
2 螺柱焊1123
2.1 常用方法1123
2.2 电弧螺柱焊1124
2.3 电容放电螺柱焊1125
3 高频焊1127
3.1 焊接过程与实质1127
3.2 分类1127
3.3 接触加热、感应加热的制管原理1127
3.4 设备及工装1127
3.5 焊接参数1129
3.6 典型产品焊接示例1130
3.7 质量检验1130
3.8 安全技术1131
4 气压焊1131
4.1 分类及特点1131
4.2 钢轨焊接1131
4.3 钢筋焊接1133
5 冷压焊1134
5.1 机理1134
5.2 方法及适用范围1134
5.3 焊接工艺1134
5.4 模具设计要求1136
5.5 设备简介1137
5.6 质量检验1138
5.7 应用实例1138
6 超声波焊1138
6.1 工作原理1138
6.2 焊接方法1139
6.3 设备简介1140
6.4 焊接接头设计形式1141
6.5 超声波焊接工艺1141
6.6 工艺因素对焊接质量的影响1143
7 扩散焊1143
7.1 方法及设备1143
7.2 工艺1144
7.3 常用材料的扩散焊的焊接参数1145
7.4 缺陷及质量检验1146
8 热剂焊1146
8.1 主要材料1146
8.2 主要设备及工装1146
8.3 应用实例1146
8.4 热剂焊的质量检验1148
9 爆炸焊1148
9.1 焊接工艺1148
9.2 爆炸焊的焊接接头性能1150
9.3 缺陷和检验1151
9.4 安全要求1151
参考文献1151
第5篇 热处理工艺规范1153
第1章 钢的热处理工艺1153
1 热处理工艺分类1153
2 退火与正火(工艺代号5111和5121)1153
2.1 均匀化退火(扩散退火)(工艺代号5111d)1153
2.2 预防白点退火(消除白点退火或去氢退火)(工艺代号5111h)1154
2.3 完全退火1158
2.4 不完全退火1161
2.5 等温退火(工艺代号5111n)1161
2.6 球化退火(工艺代号5111s)1163
2.7 再结晶退火(工艺代号5111r)1167
2.8 去应力退火(工艺代号5111e)1168
2.9 正火(工艺代号5121)1170
3 淬火与回火(工艺代号5141)1173
3.1 淬火(工艺代号5131)1173
3.2 等温淬火(贝氏体等温淬火)(工艺代号5131n)1179
3.3 分级淬火(马氏体分级淬火)(工艺代号5131m)1180
3.4 两相区加热淬火1181
3.5 回火1183
3.6 淬火与回火工艺应用示例1188
4 钢的感应加热淬火与回火(工艺代号5212)1190
4.1 基本目的1190
4.2 适用钢种1190
4.3 高频加热淬火1190
4.4 中频加热淬火1196
4.5 工频加热淬火1200
4.6 高频脉冲感应加热淬火1202
4.7 双频连续感应加热淬火1203
4.8 回火1204
5 钢的火焰淬火与回火(工艺代号5213)1206
5.1 基本目的1206
5.2 适用钢种1207
5.3 准备工作1207
5.4 工艺规范1208
5.5 操作注意事项1209
5.6 后续工序1210
5.7 质量检查1210
5.8 喷嘴与水嘴设计的有关资料1210
5.9 应用举例1211
6 钢的渗碳淬火与回火(工艺代号5310-141)1212
6.1 基本目的1212
6.2 适用钢种1212
6.3 固体渗碳淬火与回火(工艺代号5311S-141)1212
6.4 盐浴(液体)渗碳淬火与回火(工艺代号5311L-141)1215
6.5 气体渗碳淬火与回火(工艺代号5311G-141)1217
6.6 真空渗碳淬火回火(工艺代号5311V-141)1225
6.7 离子渗碳淬火与回火1227
7 渗氮(工艺代号5330)1230
7.1 基本目的1230
7.2 适用钢种1230
7.3 气体渗氮(工艺代号5331G)1230
7.4 离子渗氮(工艺代号5337)1235
8 碳氮共渗淬火回火(工艺代号5320-141)1239
8.1 基本目的1239
8.2 适用钢种1239
8.3 液体碳氮共渗淬火回火(工艺代号5321L-141)1239
8.4 气体碳氮共渗淬火回火(工艺代号5321G-141)1241
8.5 离子碳氮共渗淬火回火(工艺代号5327-141)1243
8.6 典型工件应用举例1243
9 氮碳共渗1245
9.1 基本目的1245
9.2 工艺方法1245
9.3 适用钢种1245
9.4 气体氮碳共渗1245
9.5 离子氮碳共渗1248
9.6 盐浴氮碳共渗1249
9.7 应用举例1252
10 渗硫与渗硅1253
10.1 渗硫1253
10.2 渗硅1255
11 渗硼(工艺代号5350B)1256
11.1 基本目的1256
11.2 适用钢种1256
11.3 工艺方法1257
11.4 应用实例1262
12 其他化学热处理1263
12.1 其他多元共渗(热处理工艺代号5370)1263
12.2 渗金属1270
12.3 复合渗金属1276
13 激光淬火(工艺代号:5215)1276
13.1 工艺特点1276
13.2 应用1276
13.3 适用钢材1276
13.4 准备工作要点1276
13.5 工艺要点1278
13.6 质量检查1280
13.7 应用实例1280
14 钢的冷处理(工艺代号:5131z)1281
14.1 基本目的1281
14.2 适用钢种1281
14.3 应用1281
14.4 工艺1281
14.5 冷处理工艺的发展1282
14.6 应用实例1282
参考文献1283
第2章 铸铁热处理工艺1284
1 灰铸铁的热处理工艺1284
1.1 退火1284
1.2 正火1286
1.3 灰铸铁件的淬火与回火1287
2 白口铸铁的热处理工艺1290
2.1 去应力退火1290
2.2 淬火与回火1290
2.3 等温淬火1291
3 球墨铸铁的热处理工艺1292
3.1 退火1292
3.2 正火1292
3.3 淬火与回火1295
3.4 等温淬火1298
4 可锻铸铁的热处理工艺1300
4.1 白心可锻铸铁的脱碳退火1300
4.2 黑心可锻铸铁的石墨化退火1300
4.3 球光体可锻铸铁的热处理1301
4.4 球墨可锻铸铁的石墨化退火1303
第3章 非铁金属和合金的热处理工艺1305
1 铜和铜合金的热处理工艺1305
1.1 去应力退火1305
1.2 再结晶退火1305
1.3 均匀化退火1306
1.4 固溶处理及时效1307
1.5 淬冷硬化和回火1307
2 铝和铝合金的热处理工艺1308
2.1 变形铝合金的热处理1308
2.2 铸造铝合金的热处理1313
3 钛和钛合金的热处理工艺1314
3.1 退火1314
3.2 固溶和时效强化1318
4 镁合金的热处理工艺1319
4.1 镁合金的热处理状态和代号1319
4.2 镁合金的退火1320
4.3 固溶处理与时效1320
参考文献1322
热门推荐
- 1447244.html
- 2880748.html
- 3887695.html
- 238068.html
- 984601.html
- 1842086.html
- 2720908.html
- 409221.html
- 2819019.html
- 941258.html
- http://www.ickdjs.cc/book_2909525.html
- http://www.ickdjs.cc/book_3605582.html
- http://www.ickdjs.cc/book_1598738.html
- http://www.ickdjs.cc/book_603793.html
- http://www.ickdjs.cc/book_3578900.html
- http://www.ickdjs.cc/book_579313.html
- http://www.ickdjs.cc/book_1465878.html
- http://www.ickdjs.cc/book_1398354.html
- http://www.ickdjs.cc/book_3486965.html
- http://www.ickdjs.cc/book_1419761.html